How does the ERP system handle length control of timber products?
Table of Contents
When buying, stocking and selling timber products, along with other length controlled items like metal beams, there are a number of options on how to manage them within your trading and stock management (ERP) system. With timber being an item that a customer may want to buy a number of different lengths, or order a total running meterage that is supplied from a number of different lengths it is useful to be able to hold the multiple lengths of a product with the same cross section within one product record.
On fixed size item per product
Some businesses may wish to hold each timber product with three fixed dimensions. This has the benefit of making the product easy to trade as a ‘unit’ item, meaning it can be purchased, stocked and sold as a number of units, but because the dimensions and a weight factor can be setup against the product you can still see the total Volume and Weight in stock, or on an order.

The drawback to fixed sized item timber is when the order processing becomes more advanced. For example it is not possible to purchase a Pack with multiple lengths of timber in, and if a purchase is placed for a general quantity (e.g. 10m3, or 1,000 metres) then that would need to be split into multiple products on receipt if they are of different lengths.
Similarly if a customer places an order for multiple lengths of the same cross section of timber then each fixed size item would need to be a separate line on the order.
Fixed Cross Section, Variable Lengths per product
A more flexible way to manage timber products, particularly Softwoods, is to use a variable length product. This has a fixed thickness and width to the timber, but can hold multiple variable lengths of that timber within the one product record.
The benefits to this approach are simpler order processing, including purchasing in variable length packs, general quantities, and making sales of multiple lengths on a single order line. The sales team also benefit from being able to view all the lengths available in stock on a single screen display.
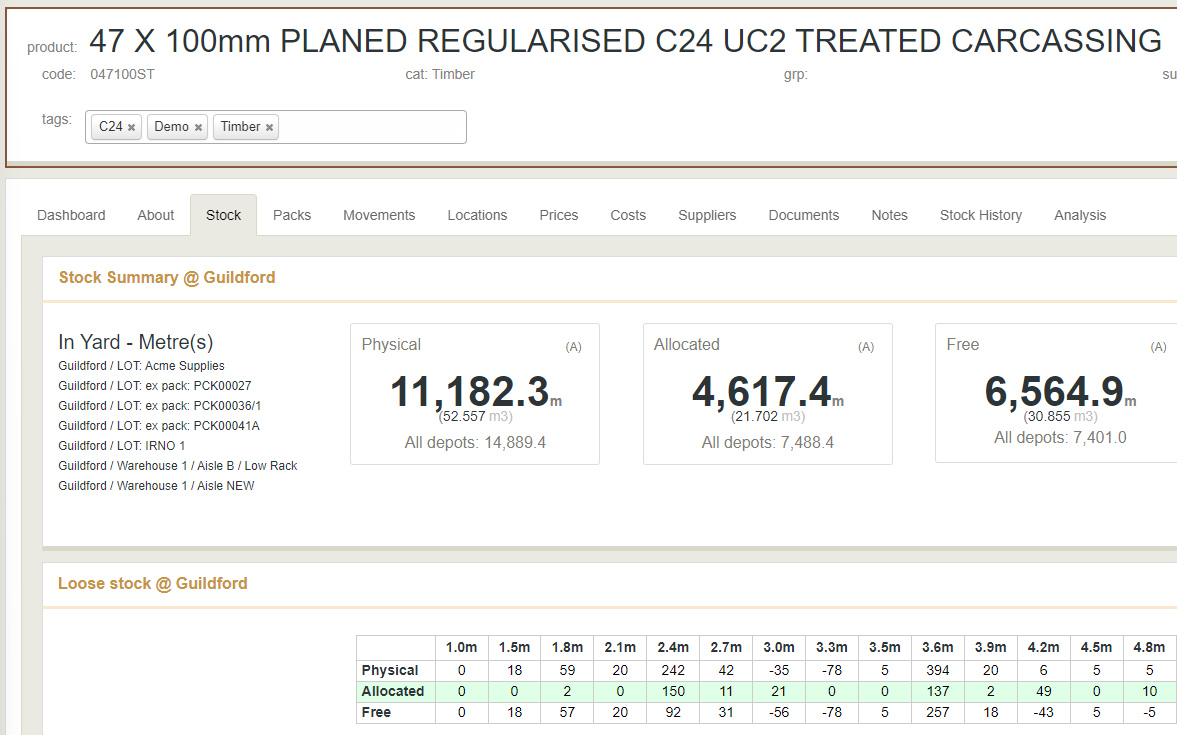
With a system designed for timber trading the variable lengths will be held on the database of the system in a flexible table, so you can record any lengths held in stock, or required for selling/milling, not just adding a text description of the lengths required.
This ‘specification’ or ‘tally’ table is quick to reference to give a live stock position, without needing to drill into lots of product records. It also means you don't need to setup a new product record (or mis-record on an existing product) if a customer wants a bespoke length of a product.
Sales orders can also be entered more quickly as you can enter the full specification/tally of lengths the customer is requesting in a single quantity entry:

The drawback to a variable length product is it is more difficult to know the price per piece, as opposed to a price per m3 or meter for the order line.
More advanced timber handling
Fixed size and variable length items work well for softwoods and sheet materials. For more advanced stock management on higher value products, that come in more unique sizes, there are stock methods that can have one fixed dimension (mixed width) or three variable dimensions (mixed size) against the product. Each requires more detailed recording as the product is purchased, stocked, milled and sold, but provides a richer level of live and historic detail about the trading of that product.